Affordable Packaging Machine Repair Services to Extend Equipment Life
Affordable Packaging Machine Repair Services to Extend Equipment Life
Blog Article
The Ultimate Overview to Packaging Device Repair Service: Maintain Your Workflow Running Efficiently
In the realm of packaging, the effectiveness of procedures pivots substantially on the integrity of equipment. Recognizing the intricacies of packaging machine repair is essential for preserving ideal performance and reducing interruptions. Regular maintenance not only expands the life of these machines yet additionally addresses usual concerns that can hamper efficiency. As we check out the nuances of troubleshooting and the crucial decision-making process between fixing and substitute, it ends up being clear that a positive method can yield substantial advantages. What certain approaches can companies carry out to ensure their packaging procedures stay continuous?
Relevance of Routine Maintenance
Routine maintenance of product packaging devices is crucial for making sure optimal efficiency and longevity. By applying a structured upkeep schedule, drivers can identify prospective issues prior to they rise into substantial issues. This aggressive method not just minimizes downtime however additionally prolongs the life-span of the equipment, eventually leading to decreased functional costs.
Routine examinations allow for the evaluation of critical elements such as seals, sensors, and belts. Dealing with deterioration without delay avoids unforeseen failings that can disrupt production and cause pricey repairs. Additionally, regular upkeep aids make certain compliance with industry requirements and guidelines, cultivating a safe workplace.
Furthermore, upkeep tasks such as lubrication, calibration, and cleansing significantly enhance machine efficiency. Improved performance translates to consistent product quality, which is important for maintaining customer complete satisfaction and brand online reputation. A well-kept packaging equipment operates at optimum rates and lowers material waste, adding to total performance.
Typical Packaging Device Issues
Packaging machines, like any kind of intricate equipment, can encounter a selection of usual problems that may hinder their efficiency and effectiveness - packaging machine repair. One common problem is irregular securing, which can cause product spoilage and wastefulness if plans are not appropriately sealed. This frequently arises from misaligned elements or worn securing aspects
One more frequent issue is mechanical jams, which can happen because of foreign items, worn components, or incorrect placement. Jams can create delays in production and rise downtime, eventually influencing overall productivity. Additionally, digital malfunctions, such as failing in sensors or control systems, can lead and disrupt procedures to unreliable measurements or irregular device actions.
Additionally, issues with product feed can additionally occur, where things may not be supplied to the packaging location regularly, creating interruptions. Wear and tear on belts and rollers can lead to suboptimal efficiency, calling for immediate interest to protect against further damage.
Recognizing these typical problems is essential for maintaining the stability of product packaging procedures, guaranteeing that machinery runs smoothly and successfully, which consequently helps in meeting production targets and preserving item top quality.

Repairing Methods
Efficient troubleshooting strategies are necessary for quickly addressing concerns that occur with product packaging makers. A systematic strategy is important for identifying the origin of breakdowns and reducing downtime. Begin by collecting info concerning the signs observed; this might include uncommon noises, functional hold-ups, or error codes presented on the device's user interface.
Next, describe the machine's handbook for troubleshooting guidelines details to the model concerned. This source can provide beneficial understandings into typical problems and advised diagnostic actions. Utilize visual examinations to check for loosened links, worn belts, or misaligned elements, as these physical variables frequently add to functional failures.
Carry out a procedure of elimination by testing specific machine functions. For example, if a seal is my site not creating correctly, evaluate the securing device and temperature level settings to identify if they meet functional requirements. Paper each action taken and the outcomes observed, as this can assist in future troubleshooting efforts.
Repair work vs. Replacement Decisions
When confronted with tools breakdowns, determining whether to replace a product packaging or fix equipment can be a facility and important option. This decision rests on numerous key factors, consisting of the age of the equipment, the degree of the damage, and the projected influence on functional effectiveness.
Firstly, take into consideration the maker's age. Older machines might require more constant repair work, leading to greater advancing prices that can surpass the financial investment in a new system.
Operational downtime is an additional crucial factor to consider. Spending in a brand-new learn this here now device that uses enhanced efficiency and dependability could be more prudent if fixing the machine will trigger long term hold-ups. Furthermore, think about the schedule of components; if replacement components are difficult to find by, it may be extra strategic to replace the device completely.
Ultimately, carrying out a cost-benefit analysis that includes both instant and long-lasting ramifications will help in making a notified decision that lines up with your monetary restrictions and operational goals. (packaging machine repair)
Safety Nets for Long Life
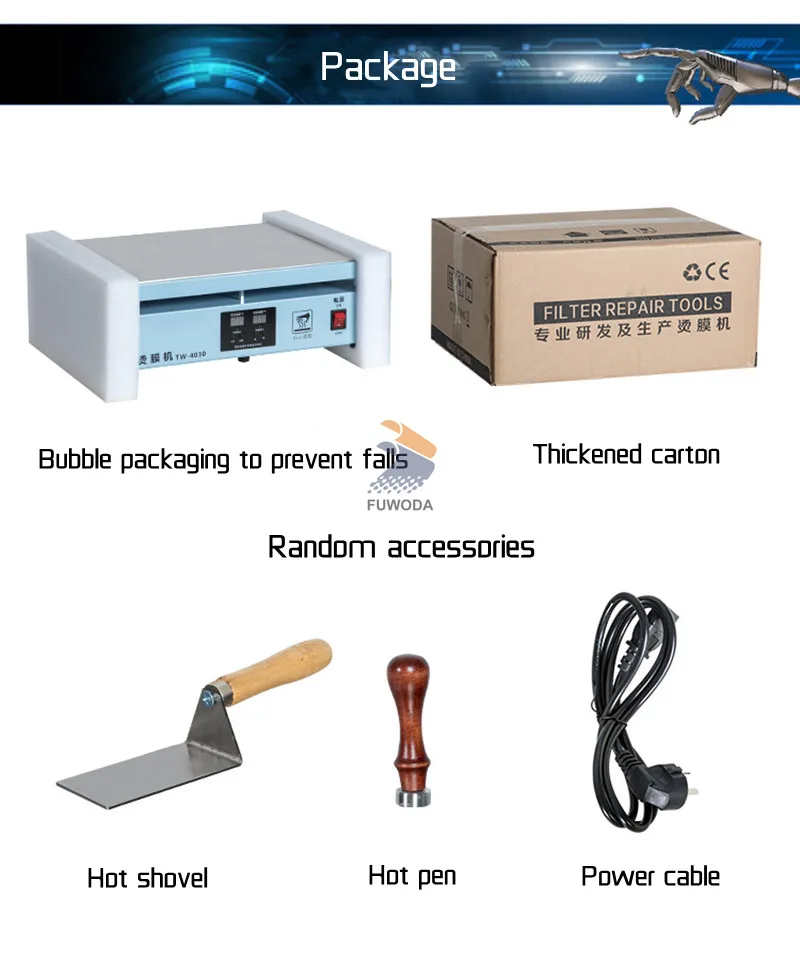
Key safety nets consist of regular lubrication of moving parts, positioning checks, and calibration of sensing units and controls. Developing a cleansing timetable to remove debris and contaminants from machinery can substantially lower wear and tear (packaging machine repair). Additionally, keeping track of operational specifications such as temperature level and resonance can assist find abnormalities beforehand
Educating team to identify indicators of wear or breakdown is one more critical part of preventative upkeep. Encouraging drivers with the understanding to do fundamental troubleshooting can result in quicker resolutions and reduce operational interruptions.
Paperwork of maintenance activities, including solution records and evaluation findings, fosters liability and promotes educated decision-making relating to repair work and replacements. By focusing on safety nets, businesses can guarantee their product packaging makers operate at peak efficiency, eventually resulting in increased performance and minimized operational prices.
Final Thought
To conclude, the effective upkeep and repair work of packaging makers are critical for maintaining operational efficiency. Routine maintenance minimizes the danger of usual problems, such as inconsistent securing and mechanical jams, while systematic troubleshooting methods help with punctual resolution of malfunctions. Mindful consideration of repair service versus replacement decisions adds to affordable monitoring of resources. By carrying out safety nets, organizations can enhance maker longevity and guarantee nonstop productivity in packaging procedures.
Recognizing the details of packaging maker repair service is essential for maintaining optimal performance and reducing interruptions.Regular maintenance of packaging devices is critical for making certain optimum efficiency and durability.Packaging devices, like any kind of complex machinery, can run into a range of typical problems that may impede their efficiency and effectiveness. If repairing the machine will certainly cause long term hold-ups, spending in a new maker that uses improved effectiveness and dependability might be much more prudent.In conclusion, the efficient maintenance and repair of packaging devices are paramount for maintaining functional effectiveness.
Report this page